How optimizing material handling gives manufacturers competitive edge
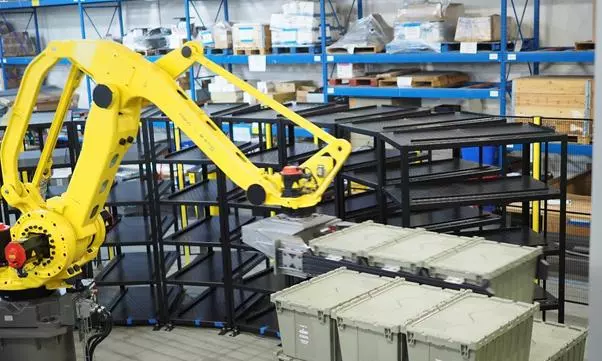
In the manufacturing industry, proper material handling is essential for the movement, storage and control of materials throughout the production process. Efficient material handling will lead to the success of any manufacturing operation as it can improve production speed, reduce waste and enhance safety. However, many manufacturers still rely on standard material handling practices that can limit their ability to be competitive in today's fast-paced market. Optimizing material handling practices can provide numerous benefits and give manufacturers a competitive edge.
Benefits of optimized material handling
Optimized material handling practices can provide several benefits that standard processes cannot. One significant advantage is increased productivity. By using advanced material handling equipment and strategies, manufacturers can move materials faster and more efficiently, resulting in faster production times and increased throughput.
Another benefit is improved safety. Advanced material handling technologies such as AGVs (automated guided vehicles) and conveyor systems can reduce the need for manual labour, reducing the risk of workplace injuries. Additionally, using technologies such as robotics and machine learning can help identify potential safety hazards and take preventive actions to minimize risks.
Efficient material handling can also reduce waste and save costs. By optimizing the storage and movement of materials, manufacturers can reduce the amount of inventory they hold, which reduces storage costs and minimizes the risk of spoilage or damage to materials. Additionally, optimized material handling can minimize errors and rework thereby reducing waste and improving product quality.
Flexibility and adaptability
In today's rapidly changing market, manufacturers must be able to adapt to changing demands quickly. Optimized material handling can provide manufacturers with the flexibility they need to meet changing market demands. By using advanced material handling technologies such as AGVs, conveyors and AS/RS (automated storage and retrieval systems), manufacturers can quickly reconfigure their production lines to meet changing product requirements. Additionally, machine learning and artificial intelligence can help optimize the movement and storage of materials in real-time, ensuring that manufacturers are always producing the right products at the right time.
Impact on speed and throughput
Optimized material handling can have a significant impact on the speed and throughput of manufacturing operations. By reducing the time required to move materials from one point to another, manufacturers can increase production speed and throughput. Advanced material handling technologies such as AGVs and conveyors can move materials quickly and efficiently, reducing the time it takes to transport materials across the production line. Additionally, technologies such as AS/RS can store and retrieve materials quickly, reducing the time it takes to access materials needed for production.
Technologies helping to improve material handling methods
Material handling is a critical aspect of manufacturing operations. As such, manufacturers continually seek ways to optimize their material handling processes and increase productivity. Fortunately, there are several emerging technologies and strategies that can help achieve this goal.
One such technology is autonomous vehicles, which can move materials around the facility without the need for human intervention. This technology can significantly reduce the time and resources required for material handling, thus increasing daily output.
Another technology that can transform material handling is palletizing. Palletizing refers to the use of machines to stack products on pallets, reducing the time and effort required for this task, and minimizing the risk of damage to the products.
AS/RS are also an advanced technology that can revolutionize material handling. These systems automate the process of storing and retrieving products, reducing the need for manual labour and increasing efficiency. Additionally, machine tending robots are increasingly being used to manage materials, especially in repetitive tasks. These robots can perform tasks such as loading and unloading machines, freeing up workers to focus on other critical tasks.
Staying competitive in the marketplace
Overall, the adoption of these advanced technologies and strategies can significantly improve material handling, increase productivity and create a safer working environment. As such, manufacturers should consider integrating them into their operations to stay competitive in the marketplace. Meeting customer expectations hinges quality products and the best fulfilment. To remain at the leading edge in their industries, clients can leverage automation technologies and strategies to reduce risk, reduce product loss, and, overall, improve efficiency and quality.
The views and opinions expressed in this article are those of the author and do not necessarily reflect the views of Indian Transport & Logistics News.
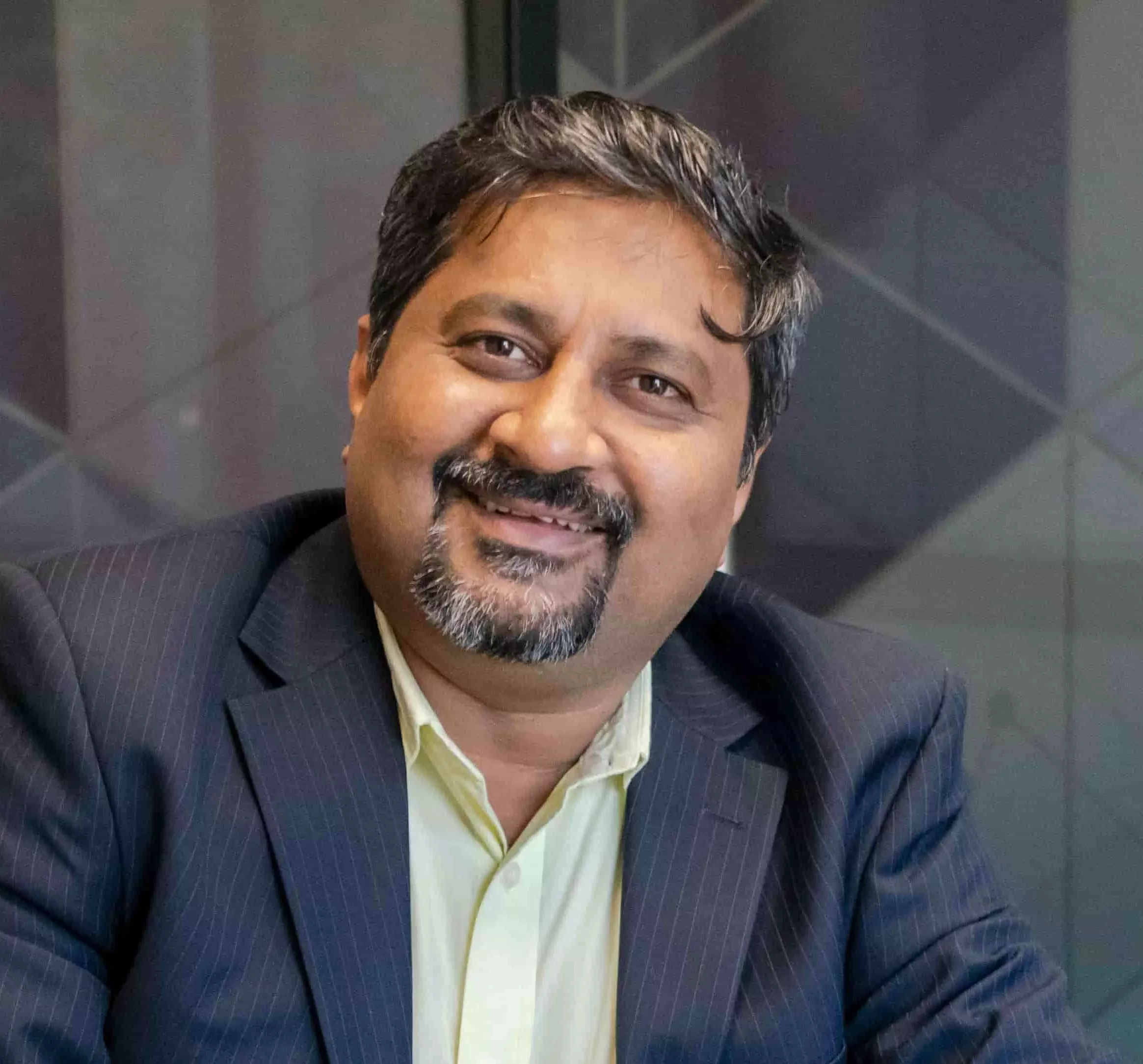
Vinayak Bhat
He is a general manager at Bastian Solutions India and has more than 18 years of leadership experience in the field of sales, operations, project execution and general management.