How advanced robotics will reshape intra-logistics
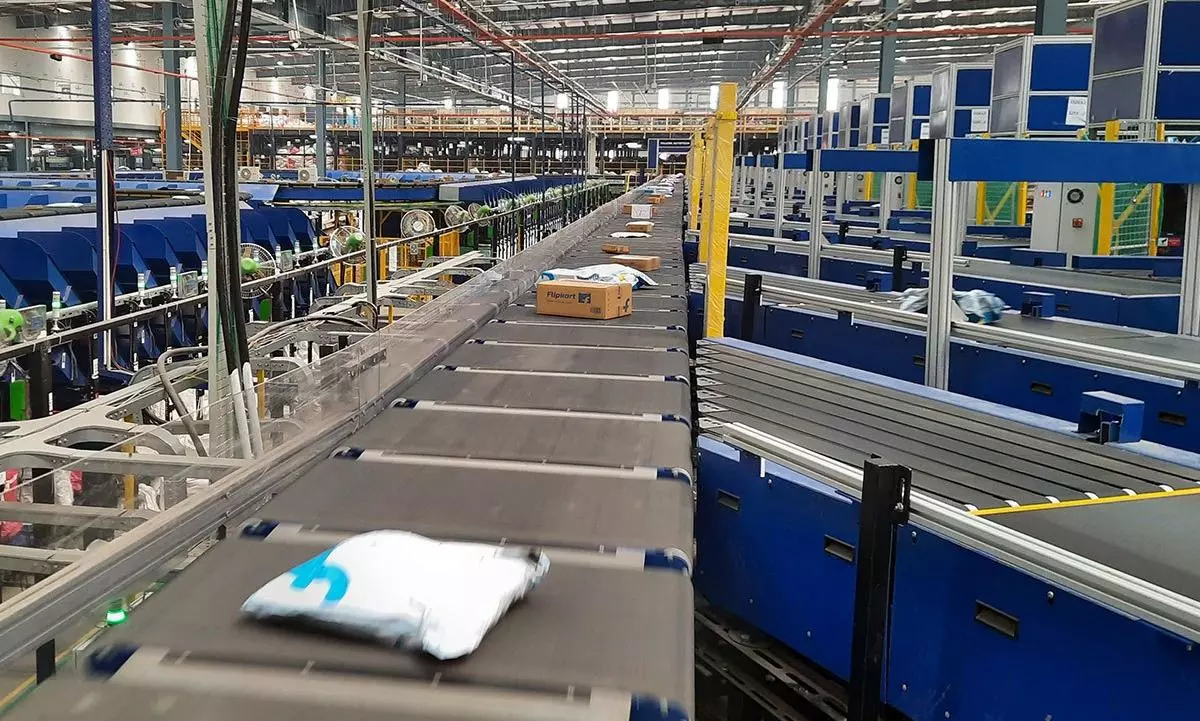
Warehousing and logistics form the backbone of the global economy, enabling the seamless flow of goods worldwide. However, traditional warehouses struggle with inefficient manual processes and rising labor costs, necessitating a tectonic shift. The latest wave of smart robotics and automation promises to revolutionize warehousing and intra-logistics by optimizing operations, reducing expenses, and future-proofing for resilience.
Industry reports estimate the current market size of logistics automation at $68 billion in 2023, anticipated to witness vigorous growth reaching around $110 billion by 2028 – indicating the extensive impact of technology and automation. The scope for transforming antiquated manual workflows in warehouses and production facilities with intelligent automation is immense. As innovation reshapes the supply chain landscape, three vital facets within the ambit of intra-logistics stand to immensely gain - internal material movements, inventory oversight and end-to-end warehouse administration.
Efficiency through autonomous material flow optimization
Internal material flow optimization forms a pivotal yet often underserved area. The journey of raw materials getting converted to finished goods via multiple production sites, the subsequent transfer to storage warehouses and finally to distribution hubs requires seamless coordination. By deploying autonomous guided vehicles and collaborative mobile robots for inter-facility container transport coupled with RFID tagged tracking, the intricate movement of items can be fluidized. Automation slashes lead times between manufacturing plants, storage depots and final mile centers - accelerating overall scheduling and order delivery. Additionally, relieving workers from manually lifting heavy loads improves workplace safety while allowing them to upgrade their skills.
Transforming inventory management with automation
Another mission-critical domain necessitating automation is real-time inventory monitoring and transparent product tracking across the supply chain. Contemporary practices centered around sporadic stock taking and manual location updates foster mismatches leading to stalled production when components run out unexpectedly. Automation mechanisms like IoT stock sensors, robotic RFID scanning and AI-powered software usher in perpetual visibility eliminating such impediments. With reliable inventory health metrics and utilization data available, predictive analytics can further fine tune future demand planning and align production cycles as well as raw material procurement to optimum levels.
Next-generation warehousing: A seamless automation focus
Lastly, a seamless automation focus extending across warehouse floors has the potential to drive step function enhancement in order processing times, storage density optimization and responsiveness to market dynamics. Collaborative autonomous mobile robots can take over repetitive tasks such as loading, sorting incoming inventory, order picking and packing freeing up human workers. Meanwhile, the combination of intelligent route-planning algorithms and AI-enabled warehouse management software establishes a data-driven system to dynamically calibrate and enhance workflows. The fusion of assisted robotics and optimisation software essentially sets the stage for next-generation facilities - smarter, faster and incredibly more flexible.
The rise of intralogistics 4.0
Intralogistics 4.0 represents the pinnacle of supply chain advancement – integrating cutting-edge technologies like IoT sensors, collaborative autonomous robots (cobots), AI/ML software, and robust Warehouse Execution Systems (WES) to orchestrate precision movement of inventory and data flows throughout the warehouse.
Intralogistics 4.0 powered facilities have advantages like greater transparency into operations, rapid traceability, responsiveness to shifts in supply-demand, and maximized efficiency in productivity and costs.
Key automation trends reshaping warehouses
Increased adoption of robotics to revolutionize warehouse efficiency by seamlessly managing warehouse processes through computer-controlled algorithms and machines. Systems such as ASRSs optimize space utilization and enhance order accuracy, reducing human error and operational costs. Meanwhile, Robotic Arms epitomize the precision and automation in manufacturing. These mechanical limbs tirelessly perform intricate tasks with speed and accuracy, enhancing productivity across industries. On the other hand, Autonomous Mobile Robots (AMR) and Automated Guided Vehicles (AGV) embody the future of material handling. These intelligent, self-navigating machines navigate warehouses and factories, adeptly transporting goods without human intervention. As technology converges in the realm of automation, the synergy between ASRS, Robotic Arms, and AMR/AGV represents a transformative force, redefining the landscape of logistics and manufacturing with unprecedented efficiency and adaptability.
Inventory visibility & traceability is an essential aspect of warehouse management. It refers to the ability to track inventory levels, movements, and transactions in real-time. Integrating autonomous mobile robots outfits managers with accurate real-time visibility while saving time and reducing human-induced errors caused by legacy manual systems. Automated warehouse vehicles provide precise traceability into pallet locations and status, which is essential for inventory management.
Production workflow automation is a strategic integration of assistive autonomous solutions that smoothly accelerates internal supply distribution and simplifies planning/monitoring of cargo movement – translating into increased factory output. This means that by using automated warehouse vehicles, factories can streamline their production processes and reduce the time it takes to move goods from one place to another. This results in increased efficiency and productivity, as well as reduced costs and errors.
The way forward
Automation and robotics spearhead innovations developing next-gen solutions for global supply chain networks. Be it large corporations or SMEs, strategic technology interventions help drive down logistics overheads and ensure efficient, transparent operations.
As warehousing forms the vital cog keeping the wheels of domestic and international trade turning, planning for automation and orchestrating AI-powered intralogistics should be the prime focal point for players big and small over the coming decade. Early adopters will gain sustained competitive advantage.
With exponential advances in robotics, IoT connectivity, AI/ML and supply chain management software, the automation revolution has truly begun. The future of warehousing shines bright with tech-enabled productivity improvements for companies ready to take the plunge into intralogistics 4.0!
The views and opinions expressed in this article are those of the author and do not necessarily reflect the views of Indian Transport & Logistics News.
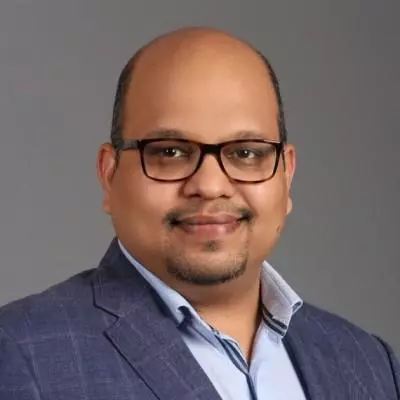
Sandeep Bansal
He is the chief business officer of intra-logistics & warehouse automation solutions provider Falcon Autotech.