Pharma shippers want logistics companies to improve workforce training
The fifth edition of the Global Pharma Logistics Summit was organised at The Leela Hotel in Mumbai on October 13, 2022.
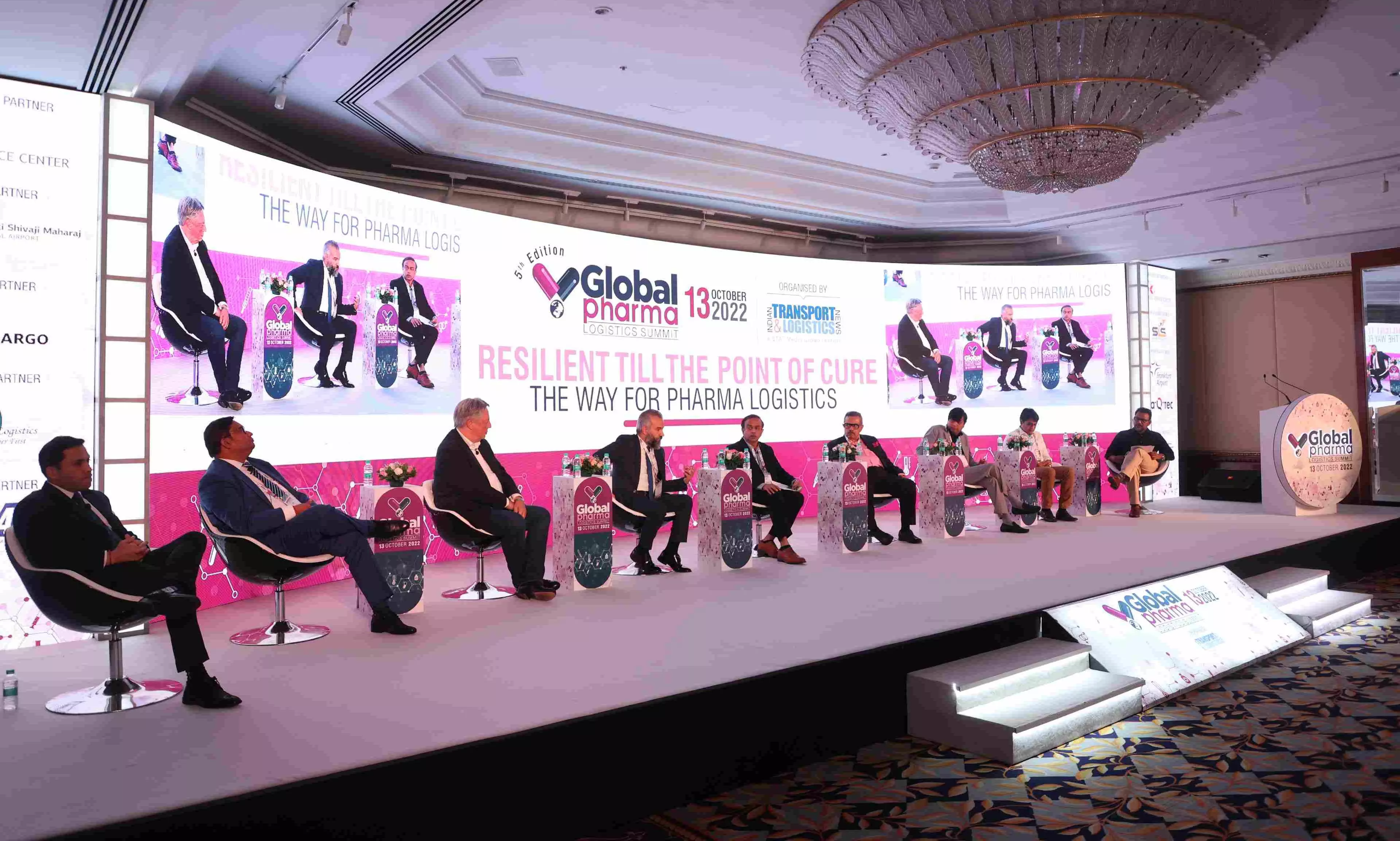
(L-R) Yashpal Sharma, Skyways Group; Manoj Singh, Mumbai International Airport - Adani Airports; Roland Weil, Frankfurt Airport; Burak Omeroglu, Turkish Cargo; Pramod Patvardhan, GSK; Tushar Jani, Cargo Service Center; Abhishek Thakur, Odyssey Logistics; Pratyush Kumar, Glenmark Pharmaceuticals; Reji John, Indian Transport & Logistics News (Moderator).
The pharmaceutical shippers or manufacturers wants the logistics industry to understand the sensitivity of the pharma product and business they are in and provide them with a better-trained workforce to handle them was the theme echoed across different panels and discussions at the fifth edition of the Global Pharma Logistics Summit.
GPLS 2022 was organised by Indian Transport & Logistics News and presented by Cargo Service Center (CSC) with Mumbai International Airport (CSMIA) as Airport Partner, Turkish Cargo as Airline Partner, Odyssey Logistics as Solutions Partner, Skyways Group as Supply Chain Partner, Skye Air Mobility as Delivery Partner, va-Q-tec and Frankfurt Airport as Supporting Partners and WIZ as the Associate Partner.
While delivering his welcome note, Tushar Jani, Group Chairman, Cargo Service Center noted that they are expanding their knowledge base to cell therapy and other pharmaceutical shipments that need special handling requirements.
"The pharma world is changing quite rapidly. Lifescience is going to be in different forms. We are going to see many cell centres coming up in many parts of the country. People are going to come to these cell centres, get cell therapy and go home. These therapies need to be delivered within two hours," he said.
While noting that this is really an exciting time for India, he said that it is also time for Indian pharma to come out with an integrated supply chain out of India.
"It is not what have to do. It is what we can do," he added.
Dr P.B.N.Prasad, Joint Drugs Controller (India), Central Drugs Standard Control Organisation (CDSCO) spoke about how CDSCO is operating as a pivotal organisation for the pharma industry and its logistics services by increasing its presence in ports and airports, integrating with various systems, adopting online approval processes.
"To reduce timelines we have worked in tandem with the customs and adopted risk-based inspections, and risk-based sampling and enabled ease of business. We have reduced the regulatory compliance burden for the pharma and its logistics industry," he said.
He mentioned the enhancement of testing capabilities at ports, especially the mini-testing laboratories for testing drug samples being imported.
He said, "It's challenging to manage the import and export of drugs and vaccines."
But he noted that the National Logistics Policy will help the pharma industry to reduce the logistics burden.
"We will see better results in terms of cost and the reduction of logistics burden in the pharma industry due to NLP," he said.
Shippers expect a better-trained logistics workforcePramod Patvardhan, API Regional Supply Head, External Supply, Global Supply Chain, GSK shared some of the learnings that he had during the pandemic.
He said, "The problem for most of us was visibility because we need to connect from supplier's supplier all the way up to our secondary markets. Before the pandemic, everybody was working in silos. It was important to bring all of them together in the interest of the patients. That was the biggest learning: how we can have that visibility, how we are all connected, have the right inventory across the supply chain nodes, invest in the right technologies, and people."
Pratyush Kumar, GM, demand planning and logistics excellence, Glenmark Pharmaceuticals reported that demand for logistics partners has also increased since the pandemic due to how it brought supply chain issues to the forefront.
"Our goods are very quality and temperature sensitive. We have to do data monitoring throughout the journey from manufacturing to end consumer. Technology plays a crucial role here," he said.
He also expressed his expectation from the logistics industry which is to have more trained people.
"The monitoring has to be right from the warehouse to airports to inside the aircraft and especially when they are on the tarmac. From my observation that is one place where good training is required. Good distribution practices have to be trained and imbibed as a culture among all the logistics partners," he said.
Responding to the shippers Jani noted that CSC is the only cargo-handling company that has employed pharmacists and he mentioned how they are training the people to empathise with the patients. While addressing the need for visibility, he said that it should start from the shippers and mentioned their ability to enable visibility from the piece level.
"Integration and visibility are the collaborative pieces of the puzzle. It starts from the shipper. How much you would tell us about the product, the processes and how critical it is? Give us those inputs we are ready to incorporate and move in. I can give you the visibility on a piece level even to the end consumer but you have to provide further visibility about what is inside the box and that should start from your manufacturing plant," he said.
On the same line about training, Yashpal Sharma, Managing Director, Skyways Group, said, "One of the most crucial and underappreciated aspects of logistics is training. Training is critical, and we put in a lot of work to train our employees in everything from commercial to handling team."
One of the learning that Burak Omeroglu, VP – Sales, Middle East and South Asia, Turkish Cargo, noted was that the logistics and air cargo industry was slow in adopting collaboration and digitalisation techniques which the pandemic changed.
"We were discussing a lot but there was hesitancy to embrace those. But with all the positive changes due to the pandemic and if we continue to walk on the same path we will be in a much better position soon," he said.
From the airport side, Roland Weil, VP – Sales, Cargo, Frankfurt Airport, raised the lack of collaboration between certain stakeholders like the ground handlers and the ramp handlers and the lack of a trained workforce as key challenges. While he mentions the general market conditions, he also noted that pharma shipments were never affected.
Agreeing with Weil on that lack of communication, Manoj Singh, SVP & Head – Cargo, Mumbai International Airport - Adani Airports, noted that they have very well-defined service level agreements (SLAs) to mitigate such issues.
"We have worked very closely with our stakeholders. We have documented the handover and takeover process, which is the grey area, and we got everybody signed. When the cargo handlers are two different companies, that is where the airports have to pitch in to see those synergies maintained. With CSC and the other three handlers, we have a very well-defined SLA in place," he said.
Meanwhile, Abhishek Thakur, managing director, Odyssey Logistics, said, "When disruption comes, how do you handle it? The only way for us was, as the going gets tough, the tough get going! That is not leaving our customers and giving them confidence in our abilities."
Gaurav Arora, Stelis Biopharma; Ugrasen Singh, Cipla; Ruby Abidi, cargo-partner; Chandan Shirbhayye, Aragen Life Sciences; Satish Lakkaraju, Wiz Freight (Moderator)
Professionalism, education, and planning
In the second panel, the discussion was around the topic "Supply Chain Therapy: Identifying pain points in pharma logistics" and touched upon the need for professionalism in the trucking industry, educating supply chain stakeholders about the fragile nature of pharma business and improving the logistics planning.
Talking about the pain points, Gaurav Arora, General Manager -Procurement (SCM), Stelis Biopharma pointed out the need for improvements in the surface mode of transport and more professionalism from truck drivers.
Arora expressed his positive outlook due to the Indian govt's initiative to launch the National Logistics Policy however he was also concerned about the speed with which it will be implemented.
He said, "National Logistics Policy is a great initiative from govt to have the policy to guide the logistics industry but the execution has to be in a fast manner in terms of solving the supply chain pain points on the ground."
Regarding the pharma cargo out there throughout the supply chain, Ugrasen Singh, Associate Director - Lead Imp/Exp. & Logistics Procurement, Cipla, said, "I'm very sad about how consignments are treated once they are out of the manufacturing plant. We make them with utmost care and treat them professionally. Stakeholders across the supply chain need to understand the sensitivity of the pharma business."
Responding to the pain points, Ruby Abidi, Director Air Cargo, cargo-partner, noted that they come into the picture while picking up the cargo and delivering it but she blamed the source of many problems on the planning stage.
"Issues in the planning stage can affect the entire supply chain of pharmaceuticals. We need an integrated platform to deal with this. We need all stakeholders, not just govts, to come together to solve them," she said.
- Yashpal SharmaSkyways GroupManoj SinghMumbai International AirportAdani AirportsRoland WeilFrankfurt AirportBurak OmerogluTurkish CargoPramod PatvardhanGSKTushar JaniCargo Service CenterAbhishek ThakurOdyssey LogisticsPratyush KumarGlenmark PharmaceuticalsReji JohnIndian Transport & Logistics NewsGaurav AroraStelis BiopharmaUgrasen SinghCiplaRuby Abidicargo-partnerChandan ShirbhayyeAragen Life SciencesSatish Lakkaraju
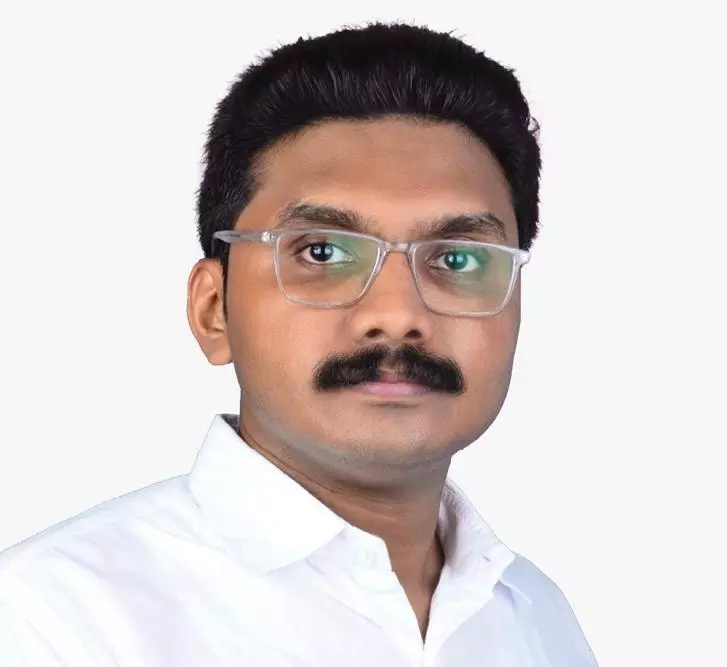
Libin Chacko Kurian
Assistant Editor at STAT Media Group, he has six years of experience in business journalism covering food & beverage, nutraceuticals and now logistics. His current passion is to understand the nuances of global supply chains and their current turmoil. Outside work, he is also interested in philosophy, history, birding and travelling. Mail him: libin@statmediagroup.com Follow on LinkedIn